The application of plastic injection molding in the automotive and electronics industries is becoming increasingly popular and important for optimizing production and enhancing product quality. With the rapid advancement of technology and growing market demands, implementing injection molding technology is crucial for businesses in these two major industries.
In modern industry, plastic injection molding has been widely applied in the automotive and electronics sectors. Injection molds allow for the creation of precise parts with complex shapes while saving time and production costs.
If you are interested in injection molds and need to produce plastic products in bulk, don’t hesitate to contact Hanoi Mould or call our hotline at 0912 308 979 for a consultation!
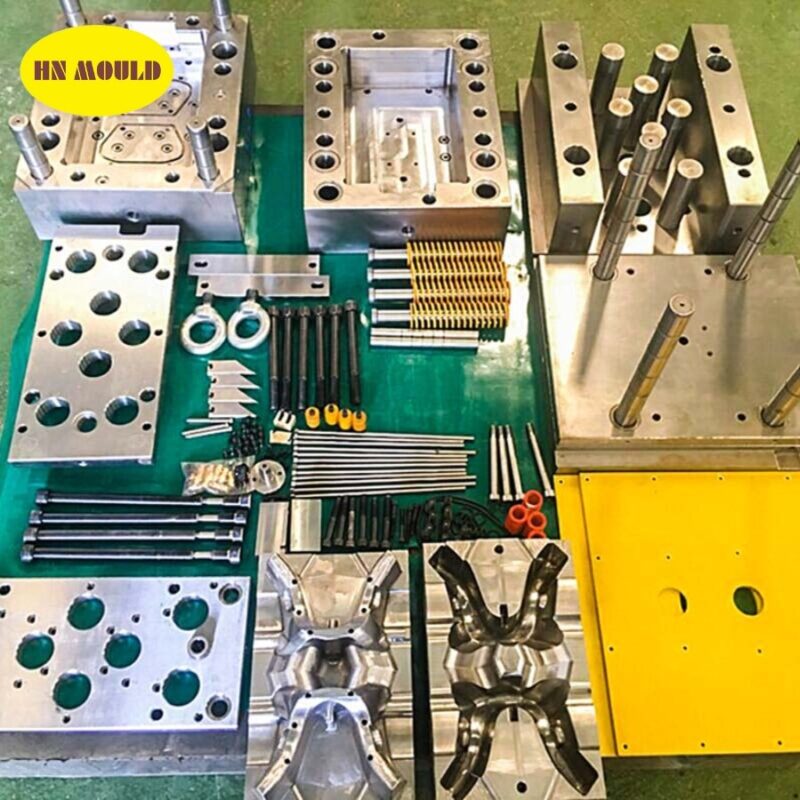
Importance of plastic injection molding in the automotive industry
Injection molding is vital in manufacturing automotive parts such as dashboards, body panels, and various decorative components.
Producing parts using injection molding allows for lighter components compared to traditional materials like metal. This not only reduces the overall weight of the vehicle but also improves fuel efficiency.
Moreover, the ability to customize designs is a significant advantage. Manufacturers can easily alter the shape or function of parts without affecting the overall production process.
Applications in the electronics industry

In the electronics sector, the application of injection molding primarily focuses on producing components such as computer casings, mobile phone housings, and various consumer devices. These components require high precision and good heat resistance.
Electronic products often demand complex designs with high levels of intricacy, and the use of injection molding helps meet these requirements. Thanks to the capability for mass production, the manufacturing process also becomes quicker and more efficient.
Challenges in injection molding applications
Despite its many advantages, the use of injection molding also faces several challenges. One of these is the issue of selecting the right materials. For each specific application, manufacturers must carefully consider to choose the most suitable material properties.
Additionally, the initial investment costs for mold fabrication can be quite high. However, when compared to the long-term benefits and profitability of the products, this remains a worthwhile investment.
Learn more about The plastic injection mold manufacturing process: https://hanoimould.com/reliable-plastic-injection-mold-manufacturing-in-vietnam/
Mass production
One of the biggest advantages of the plastic injection molding process is its ability to produce in mass quantities. Once a mold is created, producing millions of products becomes almost a seamless process.
However, to ensure product quality, monitoring and inspection processes are also essential. Manufacturers need to regularly check parameters such as thickness, color, and size to ensure they meet standards.
Materials for plastic injection molding: Optimal choices for automotive and electronics applications
Material selection is a critical factor in the plastic injection molding process. Choosing the right materials not only affects product quality but also impacts production efficiency.
Common material types

Several common materials are used in the fabrication of injection molds, including steel, aluminum, and copper.
- Steel: The most widely used material due to its high strength, wear resistance, and ability to withstand high pressure.
- Aluminum: Often used for smaller molds or prototypes due to its lightweight and ease of machining.
- Copper: Although less common, copper has excellent thermal conductivity, which can enhance production speed.
Application-Specific selection
Each type of material has its advantages and disadvantages, so the choice must be based on the specific requirements of each application.
For example, in the automotive industry, where parts must withstand heavy loads and impacts, steel is often the optimal choice. In contrast, in the electronics sector, where precision and aesthetics are more critical, aluminum and copper may be more suitable options.
Future of mold materials
With the advancement of technology, many new materials such as polymer composites and recycled materials are being researched and developed. These materials are not only environmentally friendly but also have the potential to improve production efficiency.
Trends in plastic injection molding technology for the future
The plastic injection molding industry faces numerous opportunities and challenges in the future. Embracing new trends will help businesses not only survive but thrive in a fiercely competitive market.
- Green and sustainable technology: With increasing awareness about environmental protection, green and sustainable technology is becoming an important trend in plastic injection molding production. Manufacturers are seeking eco-friendly materials and low-pollution production processes.
- Integration of smart technology: Smart technology is gradually being integrated into production processes to enhance efficiency. IoT (Internet of Things) systems can monitor production parameters in real-time, allowing for immediate decisions to optimize the process.
- Increased automation: Automation will continue to play a significant role in boosting productivity and minimizing errors in manufacturing. More automated production lines will help companies reduce labor costs and enhance production efficiency.
If you are interested in injection molds and need to produce plastic products in bulk, don’t hesitate to contact Hanoi Mould or call our hotline at 0912 308 979 for a consultation!
Conclusion
The application of plastic injection molding in the automotive and electronics industries is developing rapidly, presenting numerous opportunities and challenges. Embracing new technologies, optimizing the injection molding production process, and managing quality are key factors for business success. Above all, maintaining safety and environmental protection in production must be prioritized to ensure sustainable growth for this industry.