Contents
HDPE (High-Density Polyethylene) is one of the most widely used plastics in the world. With its flexibility and superior properties, HDPE has become the top choice in various industrial and consumer sectors. In this article, we will explore HDPE injection molding in detail, from its definition and characteristics to the manufacturing process and future trends.
If you are interested in plastic injection molds and need to produce plastic products in large quantities, don’t hesitate to contact Hanoi Mould or call our hotline at 0912 308 979 for consultation!
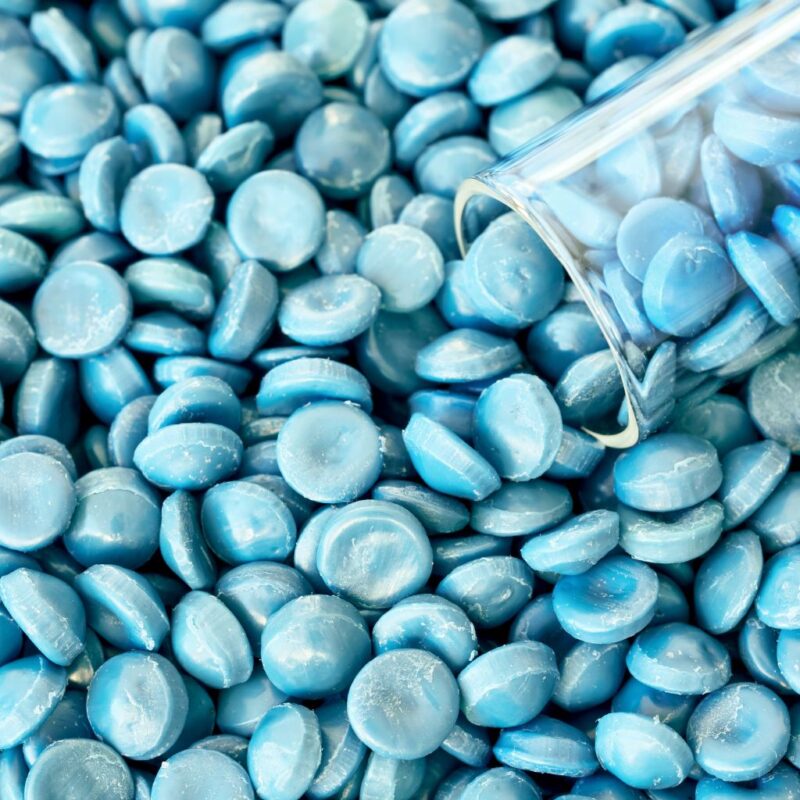
1. What is HDPE Polyethylene?
HDPE is a type of thermoplastic made from the polymerization of ethylene. With its dense molecular structure, HDPE has excellent strength and durability, making it suitable for various applications. HDPE typically comes in pellet form and can be processed into many different products through manufacturing processes such as injection molding.
Characteristics and properties of HDPE
- High strength: HDPE has superior tensile and impact strength, making it an ideal choice for products that require durability.
- Chemical resistance: HDPE is resistant to many types of chemicals, including acids, alkalis, and solvents, helping to protect products from corrosion.
- Heat resistance: HDPE can withstand temperatures up to about 120°C, but it should not be exposed to extreme temperatures for prolonged periods.
- Waterproof: HDPE is a waterproof material, making it very suitable for outdoor applications and in humid environments.
- Lightweight: With its low weight, HDPE is easy to transport and install, reducing shipping costs.
2. Advantages of HDPE injection molding
- Flexibility: The injection molding process allows for the production of products with complex shapes and diverse sizes, easily meeting market demands.
- Cost savings: Mass production helps reduce manufacturing costs and save materials, providing economic benefits to businesses.
- Fast production time: The injection molding process is quick, helping to increase production efficiency and reduce waiting times.
- Consistent products: Products are produced uniformly and accurately, ensuring high quality and compliance with international standards.
3. Limitations of HDPE injection molding
- High initial investment: The machinery and molds for HDPE injection molding can require significant initial investment, which can increase barriers to entry for small businesses.
- Recycling challenges: Although HDPE can be recycled, the process can be difficult due to the physical properties of the plastic, requiring advanced recycling technology.
- Temperature limitations: HDPE can deform when exposed to excessively high temperatures for extended periods, which needs to be considered in product design.
4. The HDPE injection molding process
The HDPE injection molding process includes the following main steps:
a. Material preparation: HDPE is granulated and fed into the injection molding machine. The material must be of good quality to avoid affecting the final product.
b. Melting: The plastic is heated until it becomes liquid (around 200-230°C), ensuring the uniformity of the material.
c. Injection into the mold: The liquid plastic is injected into the mold to shape it. The injection pressure is usually very high to ensure the plastic fills the entire mold.
d. Cooling: After the plastic hardens, the mold is opened and the product is removed. The cooling process must be carried out evenly to prevent the product from deforming.
e. Quality inspection: The final product is inspected to ensure there are no defects and that it meets quality standards.
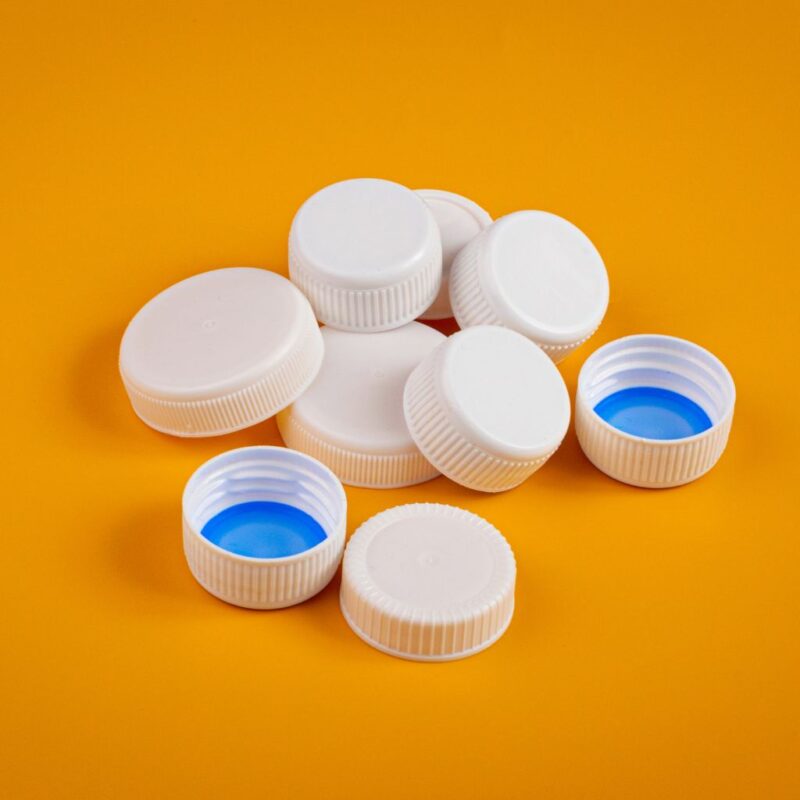
If you are interested in plastic injection molds and need to produce plastic products in bulk, please contact Hanoi Mould or call the hotline: at 0912 308 979 for a consultation!
5. Applications of HDPE injection molding
HDPE is widely used in many fields, including:
- Packaging: Production of bottles, jars, and food packaging. HDPE is a popular choice in the food industry due to its impermeability and preservation qualities.
- Household items: Production of containers, children’s toys, and other household products thanks to their durability and safety.
- Industry: Water pipes, construction accessories, and industrial equipment, due to its strength and corrosion resistance.
- Agriculture: Watering cans, storage equipment, and other products that support agricultural production.
6. Considerations when choosing HDPE injection molding
- Material quality: Choose high-quality HDPE from reputable suppliers to ensure the durability and functionality of the products.
- Mold design: Invest in a precise mold design that fits the final product to optimize the production process and minimize waste.
- Quality checks: Conduct regular quality inspections to ensure products meet standards and to promptly identify any arising issues.

Learn more about Hanoi Mold Company’s plastic mold manufacturing process here: https://hanoimould.com/plastic-mold-production-process-hanoi-mould-company/
7. Future trends in HDPE injection molding
In the future, HDPE injection molding will continue to evolve with notable trends such as:
- Recycling technology: Promoting the recycling of HDPE to minimize environmental impact and enhance sustainability in production.
- Eco-Friendly products: Developing products from recycled materials and biodegradable materials to meet consumer demand for sustainability.
- Process automation: Using automation technology and artificial intelligence to improve production efficiency and reduce labor costs.
Conclusion
HDPE injection molding is an efficient production process with many outstanding advantages. Understanding the characteristics, processes, and applications of HDPE will help businesses optimize production and develop sustainably in the future. Please contact Hanoi Mould to learn more about injection molding services and discover optimal solutions for your needs!
If you are interested in plastic injection molds and need to produce plastic products in bulk, please contact Hanoi Mould or call the hotline: at 0912 308 979 for a consultation!